近年の製造技術の向上に伴い、企業にもより高度な品質が求められる時代になりました。最新のテクノロジーを用いた改善手法も出てきていますが、品質管理の基本とも言えるのが古くから改善活動として知られている QCサークル 活動です。今回はQCサークル活動について解説します。
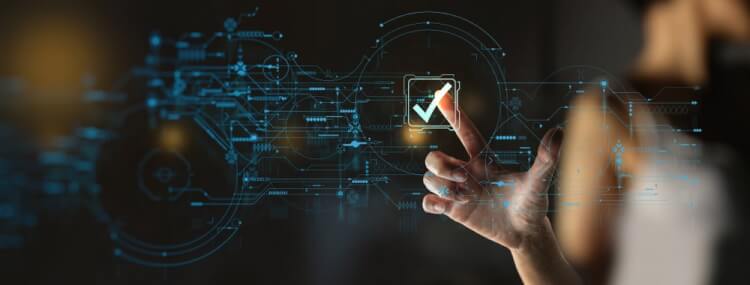
製造業における「品質向上」とは?
製造業 に関わる方にとって品質向上とは、常に意識される身近な課題でしょう。
しかし品質向上と一口に言っても対象によって意味が異なるので、議論する場合などには「何に対する品質向上か」を明確にしておかないと齟齬が生じる恐れがあります。
製品の「品質向上」
品質マネジメントを評価するISO 9000シリーズでは、製品の品質を「本来備わっている特性が要求事項を満たしている程度」と定義しています。
また、日本品質管理学会(JSQC)が定める品質管理関連用語一覧では、製品が「使う人にとっての使用目的を満たしているか知るための評価の対象(固有の性質・性能の全体)」とされます。
つまり、製品の品質向上とは、その製品の機能・特性が使う人のニーズにこたえ、より満足感をもたらすために改善されること、と定義することができるでしょう。
業務の「品質向上」
一方、業務に関する品質の場合は、対象とする内容が異なります。製品の場合は品質向上する対象が製品そのもので、「利用する人に満足してもらう製品」を作ることが目的でした。
しかし、業務の場合は、誰でも同じ品質で、失敗せず効率的に業務を行えるようプロセスやルールを改善するのが目的になります。
つまり、業務品質向上とは、業務をスムーズに実行できる状態を作ること、属人的な要素を減らして誰がやっても同じ結果を出せるようにすること、スタッフごとのバラツキを失くして業務を平準化すること、と定義することができるのです。
品質管理で重要な「QCサークル活動」とは?
品質向上を実現するための取り組みとして社会的に良く知られているのが「QCサークル活動」です。
QCとは、品質管理(Quality Control)の略で、品質管理を向上させるための改善活動のことをQCサークル活動と呼びます。
スタッフをQCサークルという小規模なグループに分け、どうやったら改善できるかを議論し実践していくことで品質管理の向上を実現していきます。似た言葉に小集団(改善)活動があり同義に扱わることが多いですが、厳密には小集団活動のひとつがQCサークル活動です。
もともとアメリカで生まれた統計的品質管理の手法が、デミング博士により日本に持ち込まれ、それを基に日本独自の改良が加えられました。
ISOが普及する前の1960~1980年代には盛んに行われた手法で、スタッフの自己啓発活動としての側面も持っていました。
当初は製造現場の改善手法としてスタートしましたが、現在では事務部門やサービス部門でも導入されています。
QCサークル活動の目的とメリット
QCサークル活動は、品質向上を実現する目的のほかにも多くのメリットがあります。
まず、現在の状況が可視化されることです。
QC活動は統計的な改善手法なので、数値で物事を把握します。そのため定量的、不良発生率など客観的に自社の状況を把握することができるようになるのです。
また、現場スタッフが主体となって自主的に改善内容を議論するため、「自分が組織をより良くしている」というスタッフのやる気アップにも繋がります。
一般的に製造部門のスタッフは、部品の仕分け、製品の組み立てなど、工程の一部分を担当し、同じ作業を繰り返し行う業務であることが多いです。そのような単調で工程の全体像が見えにくい業務を続けていくとモチベーションを維持することが難しくなります。
QCサークル活動を通じて自分が業務を改善しているという達成感や、実績を認められるという満足感を得ることができます。
また、全社で取り組むことによって、社内で情報共有化が図れるというメリットも大きいでしょう。
QCサークル活動の進め方
QCサークル活動の進め方は、データ収集→加工→分析の流れで行います。
1:テーマの選定
まずは「何を改善するのか」、その対象を明確にしていきます。例えば、定期的に不良が月に100件発生する現場があるとします。
スタッフのヒューマンエラーによる作業ミスが検査部門で頻発しているなど、その現場で何が品質を損ねる問題点になっているかを洗い出していきましょう。
この例の場合、「検査部門のミスによる不良の発生を減らす」というテーマが浮かび上がってくるはずです。
2:現状の把握及び目標の設定
次に、改善対象の現在の状況を正しく把握し、目標を設定します。データ収集はこのフェーズで行います。
データ収集に使われる手法が層別です。層別は人、システム、手順、モノ、環境、時間などの視点から分類整理する際に使われています。
たとえば、時間の視点で見ると月に不良が何件発生している、手順の視点で見ると検査の手順でミスが他の手順の1.3倍発生している、などがわかります。
つぎに、データを把握したうえで、何をいつまでに改善するかの目標を設定します。
目標設定時に使われるのが、棒グラフと折れ線グラフで作成されるパレート図です。棒グラフは不良の発生要因を発生回数の多い順に並べたものです。
そこに棒グラフの各要因発生率の累積を折れ線グラフで記すことで、どの問題を再優先に解決していくべきかを発見できます。
これは20:80の法則とも呼ばれるパレートの法則を基にしています。例えば、ある製品における不良の発生要因上位2割AおよびBが全体の8割の不良を占めているという考え方です。この場合、「AおよびB由来による不良の発生を50%減少させる」といった目標を設定できるでしょう。
3:原因の分析
どうして問題が発生したのか、考えられる理由を分析します。原因を追究するときに使われるのが特性要因図や散布図、グラフなどです。
特性要因図とは、ある問題に対してどのような要因が影響を及ぼしているかを洗い出して矢印で繋いだものです。
できあがった図の形からフィッシュボーン(魚の骨)と呼ばれます。散布図とは2つのデータの相関関係をグラフで示したものです。これらのツールを使って、原因となる要因を明確にします。ここに折れ線グラフや棒グラフなどを加えることで、より精密な原因の分析が可能となるのです。
4:対策の立案と実施
問題を改善し、目標を達成するための改善案を立案・実施します。例えば、
「検品の手順でミスが多く、結果として検品不備による不良が月80件発生している」
「検品作業は属人的でベテランのノウハウが共有されていないため、新人の検品ミスが多い」
といった状況がわかれば、
「検品マニュアルを整備し担当者に周知する」
「検品手順を簡略化する」
「一定時間ごとに休憩を挟み、長時間連続しての検品作業を行わない」
などの対策がたてられます。
5:効果の確認と発表
効果測定を行い、どれくらい改善できたかを確認をします。一度に完璧に行うことは難しいため、PDCAサイクルを回して徐々に精度を上げていきましょう。
さらに最後に取り組み内容を発表することで、社内に成果を示し情報共有を行うほか、自分達の振り返りにも役立てます。
まとめ
QCサークル活動は、現在でも品質管理、現場改善の基本となる重要な取り組みのひとつです。
自社で行うにはなかなか難しいですが、問題の把握方法や分析手法、改善に至るプロセスは参考になる部分が多いです。QCサークル活動の手法を身につけて、ぜひ、製造品質の向上を叶えてみませんか?