「倉庫業におけるヒヤリハットはどんな事象を指すか」
そのような疑問をお持ちの方に、当記事では倉庫業のヒヤリハット事例と対策を解説します。ヒヤリハットを防ぐには、原因の究明と根本的な対策が必要です。ヒヤリハットの時点で対策を実施すれば、重大な事故につながる可能性を大きく下げられます。
倉庫内を安全な職場環境にするため、ヒヤリハットの原因をなくしていきましょう。ヒヤリハットの概要
ヒヤリハットはよく聞く言葉ですが、正しく意味を説明できる人はあまりいないのではないでしょうか。まずはヒヤリハットとはどんな事象を指すのか解説します。
ヒヤリハットとは?
ヒヤリハットとは、名前の通り業務において「ヒヤリ」とする経験や「ハット」する経験を組み合わせた造語です。 ヒヤリハットは従業員の怪我や製品、機器の故障など重大な事故にはつながらなかったものの、原因の芽を摘み取っておく必要がある事象として扱われることが一般的です。
倉庫業以外では、次のようなヒヤリハット事例が挙げられます。- 製造業 :機械のメンテナンス作業で、工具が機械の隙間に落ちたものの、稼働中に異常が発生する前に発見した。
- 運送業やドライバー:車が交差点で停止していなければ、横断歩道を渡っていた歩行者と接触するところだった。
上記のように、あと一歩で重大事故になり得た事象がヒヤリハットです。
このように、ヒヤリハットは倉庫業だけのものではありません。他業界の例で、介護業界のヒヤリハットについて別記事で解説しているので、あわせてご覧ください。
介護業界におけるヒヤリハットとは | 報告書書式や事例などを解説
ヒヤリハットを防ぐことの効果
ヒヤリハットを防ぐことで、職場の安全性を向上させる効果が期待できます。
ヒヤリハットは「重大な事故にはならなかったが、一歩間違えれば大きな事故になっていた」という性質を持つ事象です。事象を防ぐには、分析や根本的な対策が必要になります。
例として従業員が転びそうになったのであれば、その原因は床に置いてあるものなのか、はたまた従業員の靴なのかによって対策が異なるでしょう。分析と対処をすることで、重大な事故につながる確率を低くできます。
職場の物理的な安全性が向上することで、従業員の精神的な安心感も高まり、業務に集中できるためパフォーマンス向上も期待できるでしょう。
倉庫業におけるヒヤリハットの事例
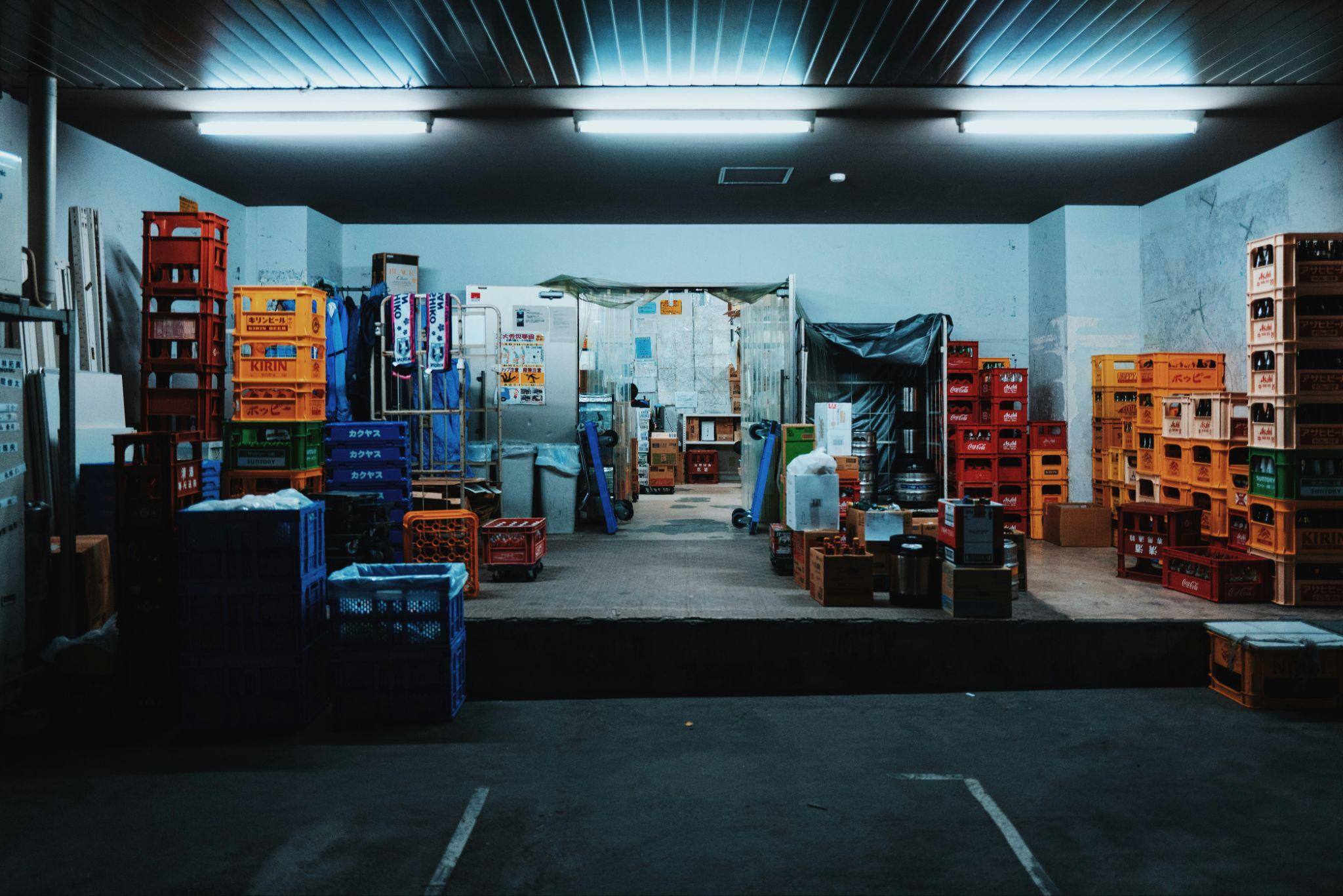
倉庫業におけるヒヤリハットの事例として以下があります。
- 倉庫の棚で作業し墜落しそうになった
- 倉庫に荷物を運ぶ際に階段で足が滑った
- 小走りをしてぶつかりそうになった
- フックが目に入りそうになった
- 積荷が崩れそうになった
- 重いものを持ち上げる際によろけた
倉庫の棚で作業し墜落しそうになった
従業員が倉庫の棚で作業し、墜落しそうになった事例です。
棚でなくても、高いところで作業をすると墜落した場合のリスクが大きくなります。従業員自身が落ちてしまい、怪我するリスクだけでなく、物を落として壊してしまうリスクや、下で別作業をしている従業員に怪我をさせてしまうリスクもあるでしょう。
人、物のどちらも墜落しないように対策をする必要があります。例として、脚立の固定やハーネスの着用、作業の半径2m以内には近づかないルールの制定などの対策ができます。
参考: 職場の安全サイト(厚生労働省)
倉庫に荷物を運ぶ際に階段で足が滑った
倉庫で荷物を運ぶ際に階段で足が滑ってしまった事象です。
従業員が怪我をするリスクや、運んでいる荷物が壊れてしまうリスクがあります。さまざまな要因が考えられますが、大きく以下に分けられるでしょう。- 荷物が多すぎる、重すぎる
- 従業員の靴が滑りやすい
- 階段が滑りやすい
荷物が多すぎる、重すぎることが原因の場合は手分けをするルールをつくりましょう。また靴や階段が滑りやすいことが原因の場合は、定期チェックや清掃などの対策が必要です。
参考: 職場の安全サイト(厚生労働省)
小走りをしてぶつかりそうになった
従業員が小走りをして、別の従業員や機器、壁にぶつかりそうになってしまった事象です。
基本的に倉庫内は死角が多く、物を運ぶ従業員や機器も多くあります。よって、急いでいても小走り禁止のルールを設定することが望ましいです。ぶつかってしまうと、怪我や荷物の破損など、さまざまなリスクが伴います。
基準が明確化されていない場合は、ルールに問題があると捉えて取り決めを定めましょう。
参考: 職場の安全サイト(厚生労働省)
フックが目に入りそうになった
従業員が高いところや離れている箇所の作業をする際に、バーについたフックが別の従業員の目に入りそうになった事象です。
フックが目に入れば失明の恐れがあります。フック自体の素材や形を変更するわけにはいかないので、従業員側が対策をすべきです。例として声掛けや、覗き込まないルールを設定することで、フックが目に近づかないよう根本的な対策をしておく必要があります。
失明した後では取り返しがつかなくなってしまうので、早い段階で対策をしましょう。
参考: 職場の安全サイト(厚生労働省)
積荷が崩れそうになった
倉庫内で積荷が崩れそうになってしまった事象です。
もし崩れてしまうと、近くにいる従業員の怪我や、積荷が壊れてしまうリスクがあります。また積荷の量によっては大きなリカバリ作業が必要になり、業務が止まってしまう可能性もあるでしょう。
積荷が崩れないようにするため、下からきちんと積み上げるルールや、機器を使って高い位置もバランスが取れているか確認するルールをつくりましょう。
参考: 職場の安全サイト(厚生労働省)
重いものを持ち上げる際によろけた
重い物を持ち上げる際によろけてしまった事象です。
もしそのまま転んでしまうと、重いものに挟まれてしまい、大怪我につながる恐れがあります。また荷物が壊れてしまう可能性もあるでしょう。従業員が「無理だ」と思ったら、直ちに別の方法を探るべきです。
対策として2人以上で持ち上げることや、機械を使って安全に持ち上げるなど、対策が必要になります。
参考: 職場の安全サイト(厚生労働省)
倉庫でのヒヤリハット対策
- 作業員同士の声掛け
- 棚や機械の固定
- 作業動線の確保
- 定期的な点検とチェックリストの活用
- ヒヤリハット発生時の報告と共有
- 作業の簡易化や自動化
- 従業員の教育
- 作業環境の監視システムの導入
作業員同士の声掛け
作業員同士の声掛けがヒヤリハットの対策になります。
倉庫内では複数人が作業をします。荷物を運ぶ場合や、機械を扱う場合は特に注意が必要です。万が一ぶつかったり、荷物を落としたりしてしまうと、怪我や破損のリスクがあります。従業員同士で声を掛け合い、安全性を確認した上で作業に取り組むべきです。
急いでいる場合に声掛けを怠ったり、返事がないのに作業を開始したりすると、取り返しがつかないことになり得るので、ルールを決めて声掛けをしましょう。
また作業以外でも従業員同士の声かけは重要です。お互いに声を掛け合うことで体調や作業内容の確認ができます。事前の共有が適切な人員配置や作業につながり、ヒヤリハットを防ぐことになります。
ヒヤリハットを防ぐためにも、たかが声かけと思わずに「されど声かけ」の意識を持ちましょう。
棚や機械の固定
棚や機械の固定により、ヒヤリハットの対策ができます。
棚や機械が固定されていないと、荷物の落下や、従業員の怪我のリスクが高まります。棚や機械を固定し、安全性が高い環境での作業を実現しましょう。
また固定されているかどうか、こまめにチェックをするルールもつくっておくことが大切です。「固定したから安全」と思わずに、従業員による定期的なチェックによって自分たちの安全性を確保するルールをつくりましょう。
作業動線の確保
作業動線の確保により、ヒヤリハットを防げます。
作業動線は従業員単位や機械単位で分けておくことで、安全性が高まり、ぶつかるリスクを抑えられます。特に荷物を運ぶ動線が重要です。荷物を運ぶ際は視界が遮られていることが多いため、周りから人や機械が近づいても気が付かない可能性があります。
作業動線を分けておき、ぶつからないよう仕組みを整えておくことがヒヤリハット対策として重要です。
定期的な点検とチェックリストの活用
機器や棚、備品の定期的な点検とチェックリストの活用がヒヤリハット対策で重要です。
作業中に機器や棚が壊れた場合でも、事故を起こすわけにはいきません。万が一事故が起こってしまった場合は、壊れた物品が悪いのではなく、壊れる予兆に気が付かなかった仕組みに問題があります。定期的な点検やチェックリストによる項目確認をすれば、壊れる予兆に気が付ける可能性が高いです。
予兆に気が付いた段階で使用をやめておけば、ヒヤリハットやトラブルを防げます。
ヒヤリハット発生時の報告と共有
ヒヤリハット発生時の報告と共有が、同じヒヤリハットを生み出さないために重要な対策です。
ヒヤリハットは対策をしていても、新たな事象が起こりえます。ヒヤリハットが起こってしまった場合は、原因を突き止めて、根絶すべきです。なお原因を従業員の注意不足や技術にしてはいけません。原因はシステムやルールなど、従業員以外に見出しましょう。
ヒヤリハット発生時の報告と共有により、社内全体に渡れば同じヒヤリハットが起こりにくくなり、安全性が向上します。ヒヤリハットの報告は、必要な項目がいくつかあるため、後述するフォーマットに沿って実施しましょう。
作業の簡易化や自動化
作業の簡易化や自動化がヒヤリハットを減らす対策になります。
ヒヤリハットは基本的に作業時に起こる事象です。よって作業自体を減らす、簡単にすることで、ヒヤリハットが起こる可能性を下げられます。例として従業員が危険な作業は機械化し従業員は機械の操作のみをする、また物を運ぶような作業は機械に任せるなど、さまざまな対応が可能です。
ヒヤリハットを防ぐため、作業自体を減らすか、簡易化する方法がないか探ってみましょう。
従業員の教育
従業員の教育もヒヤリハットを減らす対策になります。
先述したように、ヒヤリハットの原因を究明するときは社員ではなく、システムやルールから見出すべきです。従業員の作業レベルが低いことが原因になるのであれば、それは教育の方法や経験の積ませ方、仕事の割り振るルールに問題があります。
従業員の適切な教育と、レベルに合わせた仕事を任せられる仕組みを整えることで、ヒヤリハットの対策が可能です。
作業環境の監視システムの導入
作業環境の監視システム導入も、ヒヤリハットの対策に効果的です。
作業環境の監視により、危険な予兆に気が付きやすくなります。例として従業員の行動や、機器の操作に問題があれば、気が付いた監視員が指示を出すことで、問題を解消できる可能性があるでしょう。問題の解消がヒヤリハット、トラブルを防ぎます。
また機器故障の予兆を検知するための監視ツールも有効です。先述した機器や棚の定期検査を効率化できるため、効率的に安全対策ができます。
倉庫業のヒヤリハットで利用すべき報告書
倉庫業のヒヤリハットがあった場合は、大きな事故につながる前に社内全体で共有すべきです。情報の共有は、文書による報告書が効果的です。報告書の作成方法や例を解説します。
報告書の作成方法
ヒヤリハット報告書に含めるべき内容として以下があります。
- 報告日時
- 報告者
-
発生事象
発生日時
発生場所
作業内容
状況
つながった可能性がある事故 - 原因
- 根本対応策
上記を記入したら社内で共有しましょう。共有後は従業員同士で、原因や根本対応策のフィードバックが重要です。同じ事象が起こる他の原因がないか、なども含めて共有後の行動が大切な行動になります。
ヒヤリハット報告書の作成は、ヒヤリハットの事象が起こった時点からなるべく早い段階で実施しましょう。
作成は手書きでもWordなどの電子ファイルでも問題ありませんが、後から共有する際に他の従業員が確認しやすい形式にすべきです。
報告書の例
倉庫業におけるヒヤリハット報告書の例は以下のとおりです。
- 報告日時:2024年10月25日
- 報告者:佐藤 X太郎
- 発生事象:作業中、フックが別の作業員の目に近づき、接触しそうになった
- 発生日時:2024年10月24日 15:20
- 発生場所:第3倉庫 積み下ろしエリア
- 作業内容:積荷の仕分けおよび整理作業
- 状況:棚の上部にある荷物を取るために佐藤がフック付きバーを使用した。この時、山田Y男さんが棚の上部で荷物の場所を伝える役を担当していた。山田さんの指示に従ってバーを扱っていたが、場所が分からずにバーの先端にあるフックが山田さんの顔の近くを通過した。確認していた山田さんは顔をそらしたが、フックが一瞬視界に入り、ヒヤリとする場面が発生した。
- 繋がった可能性がある事故:目への接触による失明の危険
-
原因:
作業前の声掛けが徹底されていなかった
フックの取り扱いに関する明確な指示やルールが不足していた -
根本対応策:
フック付きバー使用時は、周囲の作業員に必ず声掛けを行うルールを徹底する
フック付きバーは、荷物の場所が確実に分かった状態で使用を開始する
まとめ
倉庫業のヒヤリハットについて解説しました。ヒヤリハットは重大な事故には至らなかったものの、事故につながる可能性がある重大な事象です。ヒヤリハットの時点で根本的に対応しておくことで、重大事故の可能性を下げ、安全な職場環境に近づきます。
従業員が安全に作業できる環境を整えて、高いパフォーマンスを発揮できる職場をつくりましょう。
またヒヤリハットの対策として、監視や報告書共有のためにDXを取り入れた対策も重要です。