製造業 の工場といえば、海外に生産拠点を据えて生産コストを抑えているイメージを持っている人も多いでしょう。実は近年大手メーカーを中心に工場を国内回帰する動きが業界問わず広まっています。
この記事では、製造業の工場が国内回帰している理由を4つのポイントに分けて解説します。さらに、国内回帰の課題についてもご紹介します。
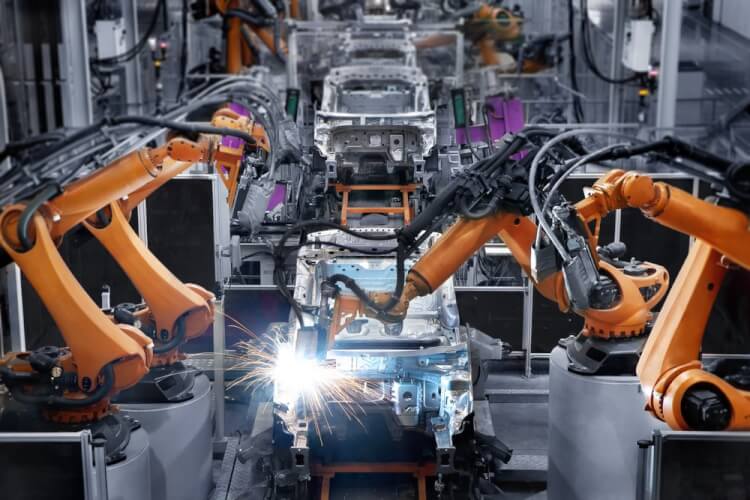
資生堂・マツダなど大手メーカーが「国内回帰」
日本の各業界を代表するメーカーである資生堂やマツダ、日清食品などが工場を国内に回帰させています。
たとえば、資生堂は2021年に福岡県で新工場を稼働させると2019年2月のプレスリリースで発表しています。2020年後半には大阪府、2021年には福岡県にも新たな生産工場を稼働させる予定です。
また、マツダは、タイで行ってきた生産機能の一部を国内に戻すと報道されています。日清食品は2018年10月から滋賀県で新工場を一部操業しており、2020年末には第3期までの工事が完了する予定です。
工場を国内回帰させている理由とは?
日本を代表する各メーカーが工場の国内回帰の動きを見せている背景にはどのような状況があるのでしょうか。以下では、4つの観点から解説します。
新興国の所得上昇
もともと、新興国を中心に生産拠点を移転していたのは、その賃金の安さにありました。
しかし、近年ではその状況も変化しており、アジアを中心に新興国における賃金は上昇しています。
これにより、新興国の消費者でも"Made in Japan"の高価格帯製品を求める消費者が増えています。言い換えると、かつては「生産拠点」として捉えていたアジアなどの新興国が、所得向上によりむしろ「消費市場」に変化しています。
また、技術移転なども含めた海外での生産におけるコスト面でのメリットが薄くなり、国内で生産を行った方がコスト効率が良いと判断する企業が増えているのです。
インバウンド需要の向上
2020年の東京五輪開催を控え、2014年あたりから「日本製」へのインバウンド需要が増加しているといわれています。
「インバウンド需要」というと、主に旅行会社や観光地の飲食店などへの訪日外国人による需要増大と考えがちですが、その恩恵は製造業にも及んでいます。
特に中国の消費者は、信頼や安心のある日本製品は多少価格が高くても、日本製であることが購入の決定要因になっています。
低価格製品への需要が高かったこともコストを抑えた海外生産拠点への移転の背景でしたが、この前提が変化しています。
日中間の単位労働コストの逆転
工場移転の要因として単純な賃金コストもありますが、単位労働コスト、つまり「生産性」も日本と海外での関係が変化しています。単位労働コストとは、生産量を同じ分増やすのに必要な労働コストです。
特に、日本と中国間ではもともと中国の方が単位労働コストは低かったのですが、今では日本の方が低くなっています。
そのため「生産性」の観点からも、国内の工場に回帰した方が合理的という判断が増えています。
日本の製造業は依然として薄利多売
工場の国内回帰自体は、単純に考えると国内の雇用が増え、その点ではメリットも大きいようにも感じられます。
しかし、海外に生産拠点を移転した背景や近年の国内への回帰に共通するのは、「生産コストの低減」です。
付加価値の高い製品を売り続けることができれば、そもそも生産コストを削減する必要がないのですが、日本の製造業は依然として「薄利多売」のビジネスを続けているのが大きな要因になっています。
つまり、大量に生産・販売をしないと利益が増えません。薄利多売で利益率が低い以上、単価や売上総額を増加させることではなく、コスト面の削減が高い優先順位になっているのです。
海外に目を向けてみると、たとえば欧州圏の製造大国であるドイツではGDPに占める輸出割合は40%程度、スウェーデンでは30%程度であるのに対し、日本では15%程度とかなり低くなっています。
一般的に、生産性が高ければ輸出額が大きくなるといわれている製造業において、GDPに占める日本の輸出割合の低さは、日本の製造業が依然として薄利多売であることの裏返しともいえるでしょう。
工場の国内回帰による課題
大手メーカー含め、増加している工場の国内回帰ですが、工場を新しく国内で稼働するうえでの課題もあります。人材リソースと用地の2つに分けて解説します。
深刻な労働人材不足
少子高齢化などを背景に、日本の人口は今後減少に向かうことは間違いないとされています。
戦後、右肩上がりに人口が増加し、それに比して工場などの生産能力を増やせば良かった時代から、減少する労働力を前提とした生産体制を構築することが大切です。
工場だけ増やしても、それを活用できる労働力を確保できなければコストが増えただけで生産、ひいては売上にはつながりません。中小企業はもちろん、大企業でさえ、人口減少を背景とした深刻な労働人材不足に直面し、工場の国内回帰における大きな課題となっています。
とはいえ、人口減少という社会環境を止めることは現実的ではなく、そのなかでも国内で工場を新しく作る場合、人手に依存せず、協働ロボットなどを活用した省力化の生産体制を構築していくのがよいでしょう。
ロボットを単なる人手の代替ではなく、人とロボットが協働して生産性を高める仕組みを作り上げていくことが重要になってきます。
国内用地の不足
工場の国内回帰を推し進めるにも、簡単に実行できるわけではありません。日本は世界的に考えても小さい面積の国で、そのなかで新たな工場用地を獲得するのは簡単ではありません。
工場用の産業用地を開発する際、大まかに開発計画の策定→各種法制の調整→用地確保→造成という流れになり、トータルで数年程度はかかります。
そのため、実際に工場を稼働したい時期から逆算して早めに準備することが重要です。
さらに、国内全体で用地が限られているだけでなく、地域レベルで用地の需給のミスマッチが起こっています。
企業の設備投資意向の高い地域では、用地を取得したい企業が多くて用地がより一層不足する一方、条件が比較的よくないエリアでは用地が余っているという状態です。
まとめ
製造業の会社が工場を国内回帰させている背景について需要・供給の両面からご紹介しました。
大きな要因として「コスト」が存在するのは変わりませんが、国内回帰の背景や課題を通して製造業が従来から抱える課題なども見えてきます。
自社がターゲットとする顧客やそのエリアなどを踏まえ、世界の潮流を見据えた意思決定が望まれます。